Why Aluminum Conductors Are Powering the Future: Benefits, Types, and Key Applications Explained
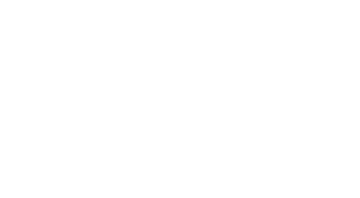
Aluminum conductor widely used in power transmission and distribution systems due to their unique combination of lightweight properties, electrical conductivity, and cost-efficiency. As industries evolve and demand more sustainable and scalable power solutions, aluminum conductors have become a preferred alternative to copper in many large-scale applications. From overhead lines to underground systems, aluminum conductors are shaping how electricity travels across the grid.
🔍 Table of Contents
-
What Is an Aluminum Conductor?
-
Why Aluminum Over Copper?
-
Types of Aluminum Conductors
-
Aluminum Conductor Properties Table
-
Real-World Applications
-
Pros and Cons at a Glance
-
Industry Standards and Specifications
-
FAQs About Aluminum Conductors
🧠 What Is an Aluminum Conductor?
An aluminum conductor is a metallic wire or cable made primarily from aluminum or aluminum alloys, designed to carry electrical current. These conductors are found in:
-
Overhead power lines
-
Distribution grids
-
Utility-scale solar projects
-
Industrial wiring
Aluminum offers excellent electrical conductivity per unit weight, making it ideal for applications where both performance and weight matter.
⚖️ Why Aluminum Over Copper?
Here’s why aluminum has gained popularity, particularly in high-voltage and long-distance transmission systems:
Property | Aluminum | Copper |
---|---|---|
Electrical Conductivity | ~61% of Cu | 100% (benchmark) |
Weight | ~30% lighter | Heavier |
Cost per kg | Lower | Higher |
Corrosion Resistance | High (oxide layer) | Moderate |
Flexibility | Good | Better |
Despite having lower conductivity than copper, aluminum’s lower density means it can deliver the same amount of current at a lower weight and cost. This is especially beneficial for aerial installations where weight directly affects structural load and support costs.
🧱 Types of Aluminum Conductors
Each type of aluminum conductor serves different applications, with variations in mechanical strength, flexibility, and temperature ratings.
1. AAC (All Aluminum Conductor)
-
100% aluminum strands.
-
High conductivity.
-
Best suited for short spans and urban areas with low mechanical stress.
2. AAAC (All Aluminum Alloy Conductor)
-
Made of aluminum alloy (usually 6201).
-
Better strength and corrosion resistance.
-
Ideal for coastal and polluted areas.
3. ACSR (Aluminum Conductor Steel Reinforced)
-
Aluminum strands wrapped around a steel core.
-
High tensile strength.
-
Commonly used in long-span transmission lines.
4. ACAR (Aluminum Conductor Alloy Reinforced)
-
Combination of aluminum alloy and reinforced strands.
-
Offers balance between conductivity and strength.
-
Preferred in high-voltage distribution.
📊 Quick Comparison Table of Aluminum Conductors
Conductor Type | Conductivity | Strength | Corrosion Resistance | Application Area |
---|---|---|---|---|
AAC | High | Low | Moderate | Urban distribution lines |
AAAC | Moderate | High | Excellent | Coastal/industrial zones |
ACSR | Moderate | Very High | Moderate | Long-span transmission |
ACAR | High | High | High | Sub-transmission networks |
⚡ Real-World Applications
Power Utilities
-
Overhead Transmission Lines: Lightweight aluminum makes large-scale transmission more economical.
-
Substations: Used for busbars and connectors due to ease of handling and cost savings.
Renewable Energy
-
Solar Farms: Used in string and trunk cabling due to cost-efficiency and thermal stability.
-
Wind Turbines: Aluminum cables connect turbines to substations, reducing weight loads on towers.
Construction & Infrastructure
-
Residential Wiring (in certain countries): For feeders and service entrance cables.
-
Commercial Buildings: Aluminum is used for power distribution to reduce installation cost.
✅ Pros and Cons of Aluminum Conductors
Advantages
-
Cost-effective: Up to 60% cheaper than copper.
-
Lightweight: Easier handling, less structural support needed.
-
Corrosion-resistant: Forms a self-healing oxide layer.
-
Recyclable: Environmentally sustainable.
-
Thermally Stable: Performs well under fluctuating loads.
Disadvantages
-
Lower conductivity: Larger diameter required for same current as copper.
-
Creep: Prone to elongation over time under mechanical stress.
-
Jointing complexity: Requires anti-oxidant compounds and proper torqueing.
-
Higher coefficient of expansion: Can affect mechanical integrity if not designed properly.
📐 Industry Standards and Specifications
Aluminum conductors must meet stringent standards to ensure safety and performance. Common standards include:
-
ASTM B231/B231M – Standard for ACSR
-
IEC 61089 – International standard for overhead aluminum conductors
-
ASTM B399/B399M – Standard for ACAR
-
ISO 9001:2015 – For manufacturer quality assurance
Manufacturers are expected to conduct type tests, routine tests, and acceptance tests to comply with regulatory requirements and customer specifications.
🙋♂️ Frequently Asked Questions (FAQs)
Q1: Can aluminum wire carry the same current as copper?
Not directly. Aluminum has about 61% the conductivity of copper, so it must be larger in diameter to carry the same current safely. However, this is typically accounted for during system design.
Q2: Is aluminum safe for residential use?
Yes, but only when installed by qualified professionals using approved connectors and anti-oxidation compounds. Aluminum wiring was controversial in the past due to poor installation practices, but modern standards have addressed these concerns.
Q3: Does aluminum conductor corrode easily?
Aluminum forms a thin, hard oxide layer that protects it from further corrosion. It is particularly resistant in marine and industrial environments when alloyed properly.
Q4: What’s the lifespan of an aluminum conductor?
With proper installation and minimal mechanical stress, aluminum conductors can last 40–50 years or more, making them a durable solution for both overhead and underground applications.
Q5: Why is ACSR used in long transmission lines?
ACSR combines the electrical conductivity of aluminum with the mechanical strength of steel, making it ideal for spanning long distances with minimal sag and high durability.
Q6: Can I replace copper conductors with aluminum directly?
Not always. It depends on the application and must consider ampacity, mechanical strength, and thermal properties. Consult an electrical engineer before replacing copper with aluminum.
Q7: What is “creep” in aluminum conductors?
Creep is the permanent elongation of aluminum over time under stress. While this is a known behavior, it can be mitigated by choosing the right alloy and tensioning techniques during installation.
🧾 Additional Insights for Professionals
Installation Tips:
-
Always use compression connectors rated for aluminum.
-
Apply anti-oxidant compounds at all connection points.
-
Ensure proper torqueing of lugs to prevent overheating.
Maintenance Advice:
-
Periodic thermal scanning can help detect hot spots.
-
Inspect for signs of oxidation at joints and terminals.
-
Use vibration dampers in overhead lines to reduce fatigue failure.
Emerging Trends:
-
Aluminum-clad copper conductors are being explored for hybrid benefits.
-
Smart grid systems are integrating aluminum more extensively due to its affordability in widespread networks.
Leave a Comment